OPTISHAPE-TS
A proactive approach to design is a game-changer for innovative development in complex automotive and manufacturing use cases. Simulating a shape’s functionality at its most upstream design stage with 1DCAE can improve design optimisation. We propose shape optimisation that links the design process from 1DCAE to 3DCAE using OPTISHAPE-TS for maximum efficiency.
OPTISHAPE-TS
OPTISHAPE-TS is a structure optimisation software for designing and developing various machine parts for brakes, motor parts, electric apparatus, construction, etc. It simulates various design and manufacturing requirements for structures that are light, strong, and possess excellent vibration characteristics.
OPTISHAPE-TS eliminates the need for human trial-and-error during Finite Element Analysis (FEA) or the enormous man-hours required for prototyping and experimentation. It also reduces material costs.
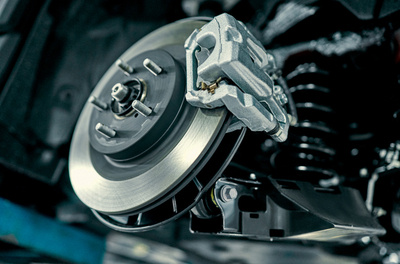
Eigenvalue control
OPTISHAPE-TS derives a shape that matches multiple eigenvalues to specified values. It’s designed using a unique “H1 gradient method”, allowing for drastic shape changes.
Developed for multiple requirements
OPTISHAPE-TS considers multiple purposes and requirements, such as stress, vibration, stiffness, volume, temperature and minimum wall thickness limit. It’s equipped with various optimisation functions to suit your needs.
Built-in analysis solver
OPTISHAPE-TS has a built-in solver. It includes various finite element solver requirements for structural optimisation.
Speed up your optimisation calculations through parallel processing.
Structure optimisation functions
You can use three kinds of structure optimisation functions with OPTISHAPE-TS:
Topology Optimisation
allows you to propose optimal layouts at the early and development stages.
Bead Optimisation
allows you to propose bead positions to increase the rigidity of the plate material.
Non-Parametric Shape Optimisation
allows you to freely deform the structure surface to propose the optimal shape.
It can be used in several examples, from the early design concept stage of development to the detailed design for improving existing products. The optimised shape can be easily transferred to CAD using the CAD model generation software "S-Generator”.
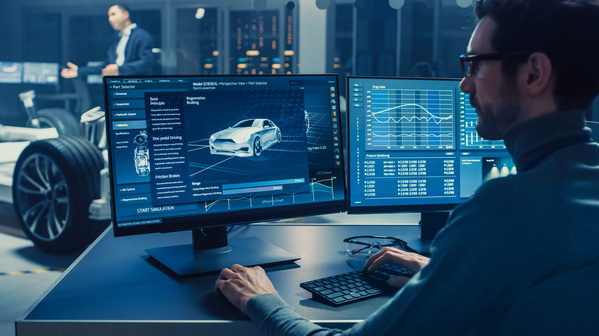
Applications
OPTISHAPE-TS has various use-case functionalities for different manufacturing industries.
For more difficult use cases, models can be modified without being bound by parametric methods, such as creating a clay model (non-parametric), where the model is visualised from scratch.
The software is notably beneficial for automotive and brake manufacturing, used for brake squeal and NV of assembly parts.
However, it can be used for various industries.
Manufacturers (i.e. brake and automotive industries, amongst others)
Weight reduction (≒ increase rigidity with the same mass)
The H1 gradient method exclusive to OPTISHAPE-TS provides even greater weight reduction than general structural optimisation software.
Control sound (avoid resonance, control natural frequency at will)
Modify the geometry with many arbitrary eigenvalues of 10 or more per part to avoid resonance. This is to a greater degree than other tools in shape optimisation.