NewtonSuite AVES
Noises and vibrations from brake friction, motors, transmissions, and other sources can negatively impact automotive companies and their suppliers. When these instances occur in the “moving living room,” companies risk being criticised by their customers.
For example, when a customer hears the "normal operating sounds" that had previously been masked by the sound of the engine for the first time, they will perceive them as "abnormal noises" and a "malfunction." The problem begins during the vibration analysis of the assembly, and when it doesn’t match the experiment due to contact parts (bolts, fittings, etc.). Discover a tool to efficiently evaluate the vibration characteristics of assemblies during simulation.
NewtonSuite AVES
NewtonSuite AVES is a design support tool that improves prediction accuracy and provides efficient evaluation of vibration characteristics, including assemblies.
Many assembly vibrations are affected by contact surface boundaries, which are often difficult to evaluate and obtain accurately. AVES provides the features necessary to evaluate such issues.
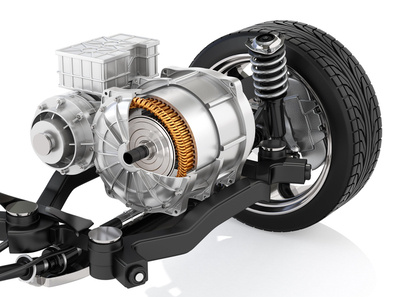
An ideal analysis and evaluation process for assembly vibration problems, including contact.
An analysis and evaluation process that uses surface pressure as a design variable.
An efficient evaluation function for comparing multiple results.
Functionalities
Boundary modelling by contact stiffness
The normal and tangential stiffness are converted from the surface pressure using the user-specified parameters.
Eigenvalue and response analysis based on contact surface stiffness
Eigenvalue analysis and response analysis can be performed by reflecting the contact surface stiffness in the model.
For example, even with the same analysis model, if the contact surface stiffness caused by the surface pressure or roughness of the boundary surface differs, the natural frequency will change.
It’s also possible to calculate the vibration response related to the surface pressure and relative displacement of the contact point.
Optional model
In addition to these standard functionalities, NewtonSuite AVES provides a MAC value evaluation to evaluate the similarity of two models, an instability evaluation (coupled strength evaluation) to assist in the evaluation of brake squeal, a similarity evaluation with an ideal mode (ideal mode comparison), and a motor option that allows you to easily create a stator laminate model. This allows you to study assembly eigenvalue analysis more efficiently.
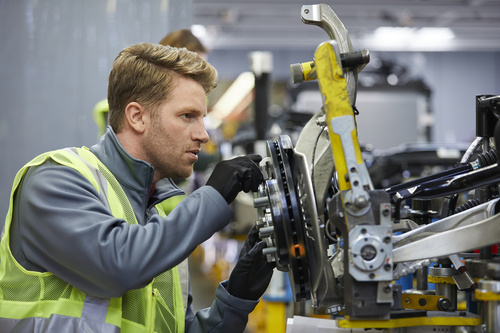
What are the common difficulties in assembly vibration analysis?
Often, when design engineers perform the vibration analysis of an assembly, the analysis doesn’t match the experience due to contact parts (bolts, fittings, etc.).
Noisy and violent vibrations from brake friction, motors, gears, and other sources can lead to poor vehicle performance and customer satisfaction. Avoid these pitfalls by anticipating these problems with NewtonSuite AVES.
Applications
NewtonSuite AVES has various use-case functionalities for different brake and automotive industries. The tool is notably beneficial for applications like,
- Bolted structures
- Motor assemblies - stator core and housing assembly
- Connectors
- Brakes
- Autobody
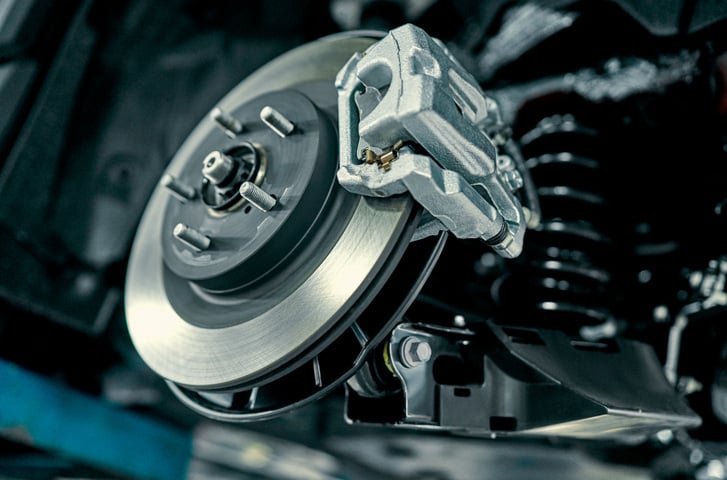